subNav_3Tier
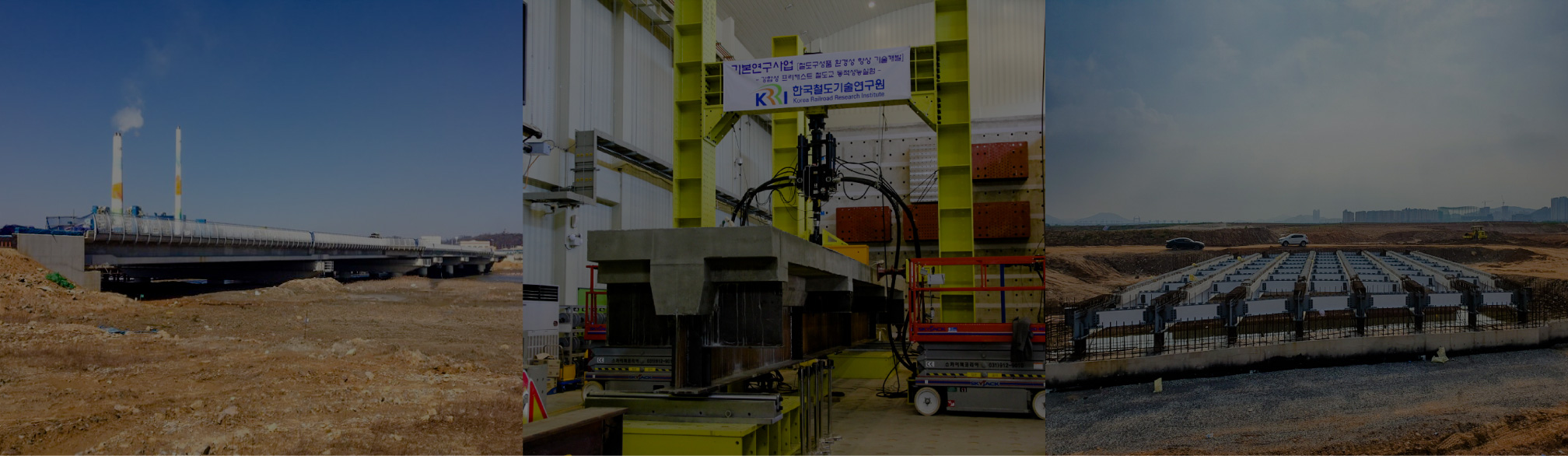
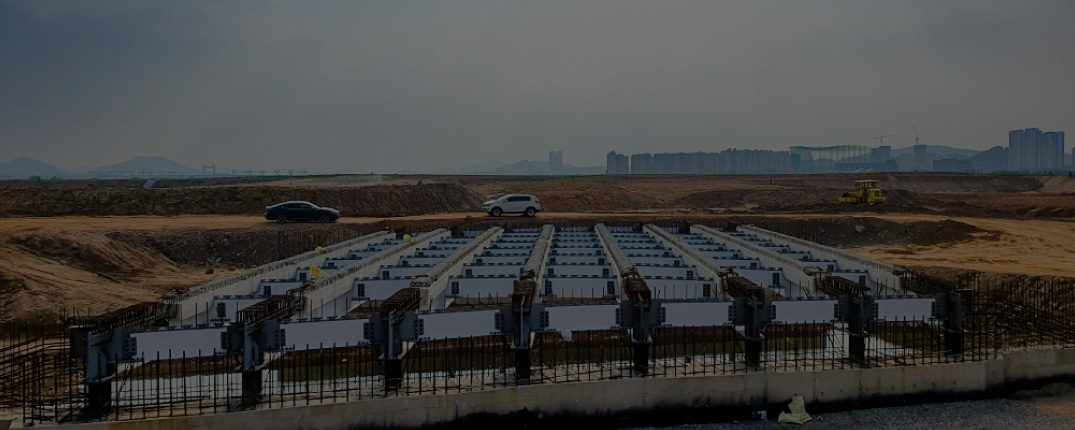
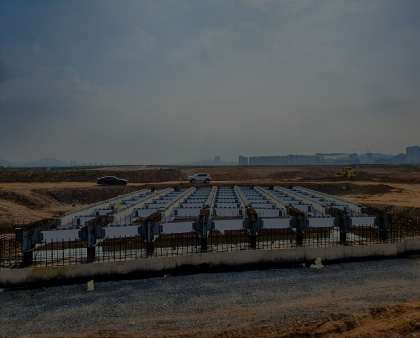
Bridge MULTICOM Girder Comparison with Similar Methods
(Based on 2014 Road Bridge Standards)
Category
Multicom Girder
Preflex Girder
Girder Cross Section
1. Concrete block production / Steel girder fabrication
2. First tensioning
3. I/G Setting
4. Non-shrink grouting
5. Second tensioning / Grouting
6. Girder erection
7. Deck concrete pouring
1. Steel girder fabrication
2. Placing on production bed
3. Pre-flexion loading
4. Reinforcement & pouring
5. Steam curing
6. Release
7. Turn over
8. Girder erection
9. Deck concrete pouring
Materials Used
■ Steel: SM490–520
■ Concrete:
- Slab, top: 27MPa
- Lower casing: 45MPa
■ PC Strand:
- SWPC 7B 15.2, Fpy = 190MPa
■ Steel: SM490–520
■ Concrete:
- Slab, top: 27MPa
- Lower casing: 40MPa
Method Overview
A composite method that combines a pre-compressed concrete panel with an I-girder. It introduces prestress in phases to compensate for long-term loss, ensuring full composite action by correcting the camber difference between the girder and panel.
Prestress is applied to the I-girder through pre-flexion loading, then concrete is cast and released, introducing compressive prestress into the lower flange concrete to create a composite girder.
Advantages & Disadvantages
- Full prestressing prevents tensile cracks in lower casing concrete
- No need for production bed installation, fast construction, and environmentally friendly (no waste)
- Partial prestressing may cause cracks in lower casing, increasing maintenance cost
- Long-term storage after compression can lead to significant prestress loss
Cost-Effectiveness
(35M)
Uses less steel (main cost driver), and the simplified process allows mass production in a short time, making it cost-effective despite being a composite structure.
(Monthly production: 20–25 units)
Steel per unit
11.7 tons/unit
Direct cost per unit
KRW 54.6 million/unit
Requires more steel during the preflexion process. Additional 7-day curing process for compressive prestressing raises overall cost.
(Monthly production: 8–12 units)
Steel per unit
21.4 tons/unit
Direct cost per unit
KRW 90 million/unit