subNav_3Tier
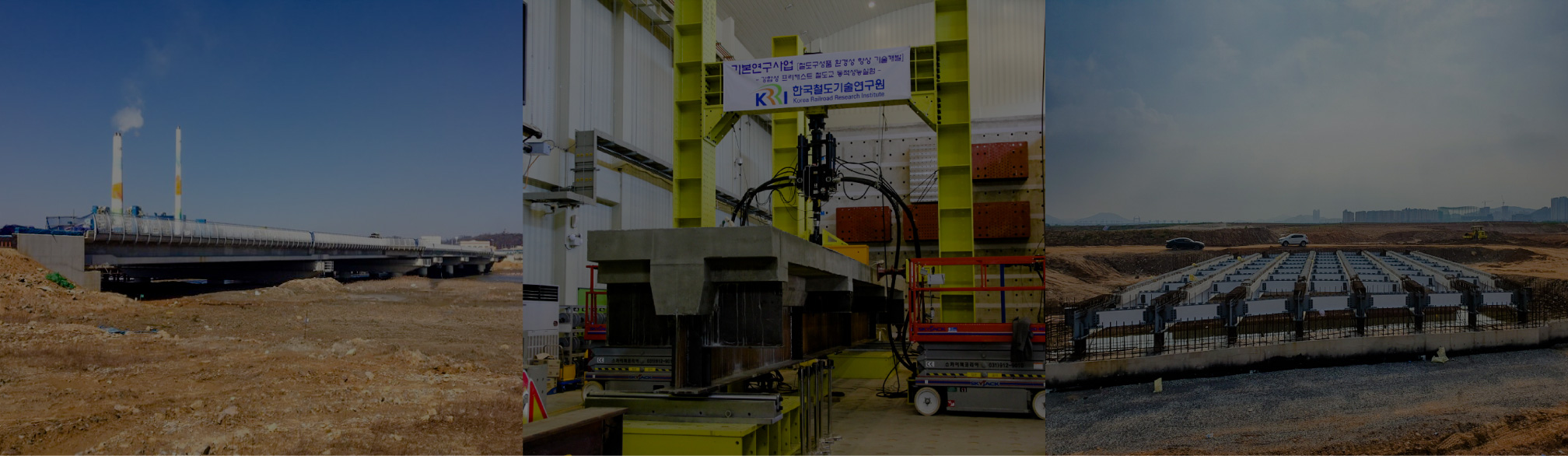
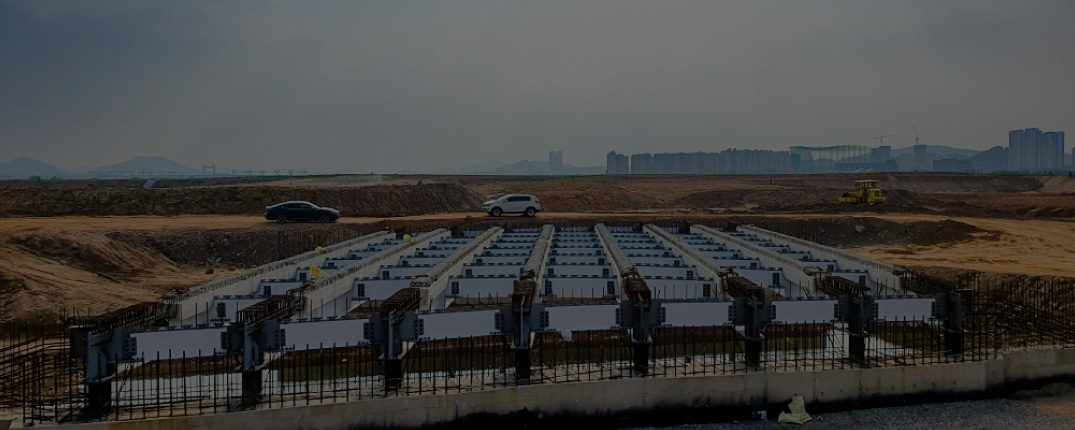
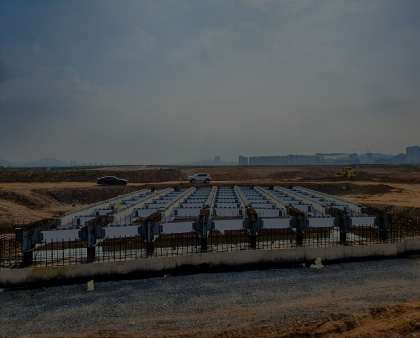
Bridge MULTICOM Girder Standard Unit Cost
(Based on 2014 Road Bridge Standards)
Category
R.P.F
E-BEAM
Girder Cross Section
1. Steel girder fabrication
2. Placement on bed
3. Preflexion
4. Reinforcement & concrete casting
5. Steam curing
6. Release
7. Strand tensioning
8. Girder erection
9. Deck slab casting
1. Bed preparation & production
2. Reinforcement & casting
3. Steam curing
4. 1st strand tensioning
5. Girder erection
6. Deck slab casting
7. 2nd strand tensioning
Materials Used
■ Steel: SM490–520
■ Concrete:
- Slab, upper: 27MPa
- Lower casing: 45~48MPa
■ PC Strand:
- SWPC 7B 15.2, Fpy = 190MPa
■ Steel: SM490
■ Concrete:
- Slab, upper: 27MPa
- Lower casing: 40MPa
■ PC Strand:
- Unbonded, mono 15.2, Fpy = 190MPa
Method Overview
A composite method using approx. 80% of the Preflexion load compared to the traditional method to induce elastic recovery in the steel I-girder and introduce initial prestress to the lower flange concrete. Additional prestress is applied using unbonded strands.
A method that enhances eccentric efficiency by integrating steel plates on the upper flange, reducing girder height. Prestress is applied at different construction stages by unifying the continuity point with steel plates + rebar + prestressing material.
Advantages & Disadvantages
- Long-term storage after compressive prestress in the lower flange may cause excessive prestress loss
- Full prestressing design ensures high crack resistance
- Wide flange makes it less suitable for curved bridges compared to PSC beams
- Full prestressing design ensures high crack resistance
Cost-Effectiveness
(35M)
High steel consumption and separate 7-day concrete curing for compressive prestressing in preflexion process increase construction cost.
Slightly less steel is required than traditional Preflex methods, but additional processes offset cost savings.
Steel per unit
19.3 tons/unit
Direct cost per unit
KRW 74.68 million/unit
Beam cost per m²
KRW 878,000/m²
Superstructure cost per m²
KRW 180,000/m²
Total direct cost
KRW 1,058,000/m²
High steel consumption and separate 7-day curing for compressive prestressing in preflexion process raise construction cost.
(Monthly production: 8–12 units)
Steel per unit
-
Direct cost per unit
KRW 33.08 million/unit
Beam cost per m²
KRW 389,000/m²
Superstructure cost per m²
KRW 180,000/m²
Total direct cost
KRW 569,000/m²
Standard
L = 35m, B = 24.3m, 10 girder rows
Design Load: DB-24